La reparación de un coche oxidado es una tarea de restauración que tiene como objetivo sanear todos los componentes afectados por los fenómenos de la oxidación y la corrosión. Así se consigue frenar la degradación progresiva del metal y alargar la vida de la carrocería. ¿Quieres saber cómo realizar esta operación para conseguir unos resultados excelentes? En este artículo compartimos contigo las recomendaciones más importantes.
La oxidación y la corrosión suceden de forma natural y son el resultado de una serie de reacciones químicas que ocurren sobre los metales cuando se ven expuestos a determinadas condiciones ambientales, térmicas o de contacto con otros metales o compuestos químicos.
Sin embargo, el efecto de la oxidación no siempre es negativo, ya que sobre ciertos metales, como el aluminio o el cobre, actúa como capa de protección del metal base.
Recomendaciones generales a tener en cuenta para reparar con éxito un coche oxidado
Las recomendaciones generales para reparar un coche oxidado son parecidas a las que se pueden aplicar en cualquier tipo de trabajo relacionado con la corrección de chapas oxidadas o corroídas:
-
Conviene asesorar a los clientes para que sean conscientes del riesgo que supone no reparar algunos daños que ocurren sobre la carrocería del vehículo.
-
Hay que seguir siempre las indicaciones del fabricante al aplicar cualquier proceso operativo, producto o pintura.
-
Se deben utilizar productos de calidad que garanticen la durabilidad de la reparación.
-
Se ha de disponer de herramientas y útiles que faciliten la tarea de reparación del coche oxidado y contribuyan a la mejora de las condiciones de trabajo y de la productividad.
-
Hay que efectuar una evaluación inicial del daño para determinar con exactitud el tipo de problema que existe. Gracias a esta recomendación es posible escoger el método de reparación, las herramientas y los productos más adecuados en cada caso.
-
Antes de aplicar cualquier producto o pintura sobre el coche oxidado, es fundamental descontaminar la superficie siguiendo estos tres pasos:
-
-
Efectuar un desengrasado inicial de la superficie con un limpiador como TEROSON VR 10.
-
Realizar un soplado o aspirado de la zona de trabajo una vez se haya terminado de lijar o cepillar.
-
Llevar a cabo un desengrasado final antes de aplicar los productos o pinturas seleccionados.
-
-
No hay que retardar más allá de lo estrictamente necesario la aplicación de masillas y aparejos cuando el metal está desnudo.
-
Se debe tratar el metal desnudo con imprimaciones anticorrosivas, especialmente en las caras internas de metales solapados.
-
Es muy conveniente complementar la protección anticorrosiva con la aplicación de revestimientos de bajos, antigravillas o ceras de cavidades en las zonas expuestas a proyecciones y acumulación de humedad, suciedad y barro.
-
Hay que sellar correctamente cualquier tipo de junta que pueda haber en la zona de reparación.
-
Bajo ningún concepto se deben emplear productos que agredan u oxiden el metal (agua, determinados ácidos, etc.).
-
Cuando no exista la certeza de que los restos de óxido se pueden eliminar completamente, se recomienda utilizar convertidores del óxido que sean capaces de anular su capacidad destructiva.
Recomendaciones específicas para reparar con éxito un coche oxidado
¿Qué debes tener en cuenta para eliminar cualquier punto de oxidación o corrosión al reparar un coche oxidado?
-
En primer lugar, es necesario determinar con exactitud qué zonas presentan óxido y cuáles corrosión, ya que el proceso de reparación es distinto en cada caso. Existe corrosión cuando una superficie metálica presenta rugosidad o irregularidades, más allá de las manchas anaranjadas-rojizas del óxido.
-
La segunda recomendación es tener presente que cualquier punto de óxido o corrosión se ha de sanear perfectamente para eliminarse por completo. De no ser así, el deterioro del material se va a seguir produciendo con el paso del tiempo.
-
Se debe aplicar el proceso de reparación adecuado a cada tipo de daño. De forma general, se dan estas tres situaciones:
-
-
Oxidación leve sin rugosidad ni irregularidades superficiales. En estos casos, en que el coche oxidado se ha llevado al taller a tiempo, basta con un lijado con grano abrasivo P-80 o P-120 colocado sobre una rotorbital de órbita 5 o 7 y plato duro.
-
Oxidación más marcada sin rugosidad ni irregularidades superficiales. Cuando la presencia de óxido es mayor, hay que emplear un disco abrasivo de púas metálicas o tridimensional colocado sobre un taladro o una cepilladora.
-
Oxidación marcada con presencia de una ligera rugosidad de la superficie (inicio de la corrosión). En estos casos, hay que optar por abrasivos que tengan la capacidad de copiar la forma de la superficie, ya que así se asegura que el abrasivo se introduzca en las irregularidades formadas sobre la superficie del metal. La mejor opción en estas situaciones es utilizar un abrasivo de cerdas de acero colocado sobre un taladro o cepilladora.
-
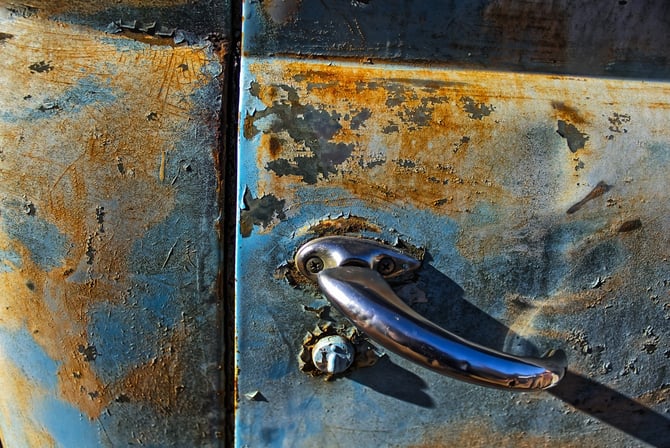
-
Corrosión avanzada. Cuando la corrosión se encuentra en un estado avanzado, es común que se haya perdido demasiado espesor de chapa. En estas situaciones, es imprescindible cepillar la superficie para eliminar cualquier resto de óxido y rellenar la falta de material con fibra de vidrio o masillas reforzadas como TEROSON UP 150. Si la pérdida de espesor es demasiado acusada, es recomendable tratar el problema como se explica en el siguiente supuesto.
-
Corrosión muy avanzada que ha provocado una falta de material. Cuando el metal ya está podrido, la única solución es reconstruir la zona dañada tras haber eliminado la parte más deteriorada. La zona podrida se puede cortar con una amoladora o sierra y el área limítrofe se debe cepillar hasta eliminar cualquier resto de óxido. A partir de ahí, la falta de material en la carrocería del coche oxidado se repone con uno de estos dos sistemas:
-
Soldando un retal de chapa por la cara interior del panel afectado. El retal debe ser de características similares a las del panel original y quedar solapado en todo su contorno para garantizar la resistencia de la reparación. También ha de estar convenientemente protegido contra la corrosión con pinturas en aerosol como LOCTITE SF 7800 o mediante toallitas conversoras como BONDERITE M-NT 1455-W. Para rellenar de forma rápida y efectiva la zona de trabajo se recomienda utilizar productos de relleno específicos como TEROSON EP 5010 TR. Este producto sustituye a los tradicionales materiales de relleno que integran estaño para aportar aportar ventajas tan interesantes como un lijado más sencillo y la eliminación de llamas abiertas para su aplicación. Otra opción es utilizar inicialmente masillas con alto poder de relleno como TEROSON UP 150, y de acabado final con masillas de textura fina, como TEROSON UP 210.
En el siguiente vídeo se muestra un ejemplo de aplicación de TEROSON EP 5010 TR.
-
Rellenando la superficie con resina acrílica y fibra de vidrio. Para ello, primero hay que generar un soporte para las distintas capas de resina y fibra. Esta base se consigue fabricando una contrachapa sobredimensionada unos 50 mm en todo su perímetro, cuando hay acceso a la cara interior, o mediante poliuretano expandible cuando no lo hay. Si se opta por la segunda opción, hay que tener la precaución de no aplicar el producto en los casos en los que existen elementos móviles cercanos que puedan quedar retenidos tras su aumento de volumen (de hasta un 50 %). Por esa expansión, tampoco se aconseja aplicarlo en demasiada cantidad.
Tras haber creado el soporte de apoyo, se rellena la superficie con sucesivas capas de resina y fibra o con TEROSON EP 5010 TR. Utilizando TEROSON EP 5010 TR se simplifica el proceso, ya que es un producto más limpio y fácil de trabajar que la resina y la fibra que, además, presenta un niveles de resistencia superiores.
Una vez seco, y para finalizar el proceso de reconstrucción de la carrocería del coche oxidado, es necesario enmasillar la zona con masillas de acabado fino que permitan cubrir la porosidad que haya quedado.
Conclusión
El óxido se puede convertir en un grave problema para la salud de la carrocería del vehículo. Por eso conviene conocer y aplicar las recomendaciones que hemos mencionado en las reparaciones de cualquier coche oxidado. Estas ayudan tanto a subsanar el problema de forma eficaz, como a prevenir que vuelva a aparecer.
Fecha de actualización: 4 de diciembre de 2023